The Basics of 3D Printing
3D printing is a radically new manufacturing technique that differs fundamentally from traditional processes such as machining, casting, forming, and molding.
It can take designers only days to go from idea to holding a prototype in their hands. Manufacturers are using it for rapid prototyping and even end-use parts. Click https://www.by3design.com/ to learn more.
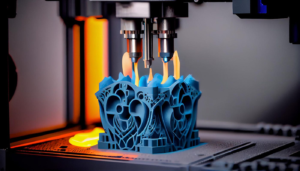
GE Aviation’s LEAP engine uses 3D-printed Cobalt-Chrome fuel nozzles, which are 25% lighter and five times stronger than conventional ones.
Materials
Several materials can be used for 3D printing, including plastics, resins, ceramics, and metals. Plastics are among the most common materials for printed objects, with a wide range of applications. The most popular plastic 3D printing materials include polylactic acid (PLA), Acrylonitrile Butadiene Styrene (ABS), polyamide (Nylon) and glass-filled nylon, epoxy resin, photopolymer resin, and wax.
Resins are also widely used for 3D printed models, and come in a number of varieties. High-detail resins are most useful for making detailed and realistic models, such as chess pieces and figurines. Transparent resins, which are available in a variety of colors, are often used to make objects that require a smooth surface or for aesthetic purposes.
Composites are usually created by combining a thermoplastic base material with other reinforcing elements like carbon fiber, fiberglass, kevlar and graphene. This helps to create stronger parts with greater strength and stiffness than the original thermoplastic materials alone.
Among the most popular metals for 3D printing are aluminum, stainless steel and bronze. These are generally printed with a process called Direct Metal Laser Sintering (DMLS), which can create highly functional prototypes and end-use parts at a much faster rate than traditional manufacturing methods.
Ceramics are an increasingly common option for 3D printed objects. This material is incredibly strong and has the ability to withstand very high temperatures, but it is difficult to work with due to its brittleness. For this reason, most printed ceramics are produced as a substitute for traditional metal parts, rather than as functional products.
In order to overcome this issue, many manufacturers are now using a technique known as Directed Energy Deposition (DED), which uses a laser or electron beam to melt and deposit the necessary materials onto the build platform. This makes it easier to produce a part with a complex structure that would be impossible or impractical to build by hand.
Graphene is one of the newer materials for 3D printing, and it offers a unique combination of properties that makes it suitable for use in a variety of different applications. Graphene is highly conductive, flexible and extremely strong without being brittle. These qualities mean that it can be used to print components for electronic devices, such as touchscreens.
Design
The design of a 3D printed object serves as the blueprint that dictates how a product will look, feel, and function. Effective designs ensure a successful result by ensuring that the final product adheres to strict specifications, possesses suitable geometries, and incorporates necessary features. Moreover, well-crafted designs optimize material utilization and printing time, improving efficiency while minimizing waste.
Unlike traditional subtractive manufacturing processes, which require a block of raw material to form a finished part, 3D printing creates a three-dimensional object by building up layers of materials in a computer-generated model. As such, 3D printing is much more cost-effective than conventional manufacturing methods.
In addition, 3D printers are capable of producing complex, bespoke geometric parts that are impossible to manufacture using traditional methods. This makes them ideal for prototyping new products or experimenting with new ideas, and it also allows manufacturers to make changes to their products more quickly than traditional production methods.
It’s important to keep in mind that different types of printing technology have different limitations. For example, FDM prints have a limited range of colors and the surface quality is inferior to other types of printing. For this reason, it’s important to choose the right type of material based on its properties and the application for which the part will be used.
Additionally, metal 3D printing requires extensive post-processing to achieve the desired finish and mechanical properties. In many cases, the metal requires heat treatment to relieve residual stresses and improve its ductility and durability. In order to minimize the need for extensive manual intervention, it’s essential to consider these requirements during the design phase.
Moreover, it’s important to consider how the finished part will be handled and stored. For example, a component that needs to be used in an environment with extreme temperatures or chemical solvents should be made out of a durable, impact-resistant material such as ULTEM or polycarbonate. Similarly, a component that is used to hold tools should be made out of an easy-to-clean plastic such as PEI or PEEK. These considerations will help to ensure the longevity of the printed component.
Slicing
The slicing process is one of the most important parts of 3D printing because it allows you to prepare a 3D model for the printer. The slicing software will break your model down into layers that the 3D printer will print successively until the object is complete. Depending on the layer thickness, you will be able to control the final surface finish and structural strength of the part.
The first step in slicing is to create a file format that is recognized by your 3D printer. Most 3D printers accept STL files, which store the visual model of the object. The slicer then uses algorithms to translate the STL file into a set of instructions that your 3D printer can understand. The final result is a G-code file, which contains the detailed instructions for your 3D printer to construct the object from its base.
As the slicing process continues, your 3D printer will build the object from the bottom up using the filament that you supply to it. The slicing algorithm will also determine whether or not the object requires support structures. Support structures, which are known as rafts and skirts, are used to support the object during its fabrication. They are usually made of multiple lines of filament that encircle the base of the object, touching it but not underneath it.
In addition to the slicing process, you can optimize your print path by controlling the number of supports and the infill pattern. This will help you save time and materials by reducing the amount of material that is wasted during the printing process. Infill density is another important parameter that can be controlled to reduce the amount of time and materials needed to make the part.
Once your slicing is completed, you can upload the G-code file to your 3D printer and begin the printing process. The slicing process is visible through the transparent panel on the Raise3D Pro2 Series printer or through the APP RaiseCloud in real-time, so you can monitor your 3D printer’s progress as it builds your model.
Printing
3D printing is a manufacturing process that does not use blocks of material to produce physical objects; it creates them by adding layers of material one at a time. 3D printing is a versatile technology that can be used across a range of industries. It is used for prototyping, tooling, manufacturing, education, healthcare, aerospace, and more.
The printing process of 3D printing involves three broad categories of technologies: sintering, melting and stereolithography. Sintering processes like direct metal laser sintering and selective laser sintering combine fine powdered materials to form high resolution parts. Melting processes like direct energy deposition, electron beam melting and powder bed fusion melt and fuse layers of thermoplastics to form parts. Stereolithography, the earliest form of 3D printing, uses lasers to cure photopolymer resin to create parts.
Once the part has been printed, it requires a bit of post-processing to prepare it for its final application. This may include sanding or smoothing for required finishes, removal of support structures and heat treatment to achieve specific materials properties. Alternatively, many parts can be finished with paints or surface coatings for aesthetics.
Since 3D printed parts are often considered a substitute for traditional manufacturing components, it is important that they meet industry and ISO quality standards. This is a key reason why the UltiMaker marketplace offers only verified and certified parts for 3D printing.
The most common use of 3D printing in the professional world is rapid prototyping. Engineers can test their designs with prototypes that look and behave like the end product, reducing development time and risk of expensive revisions. When they’re ready for production, they can use the digital design file to print a few dozen or thousands of real, functional components without the cost and lead time of conventional manufacturing techniques.
3D printing can also eliminate the need for warehousing or inventory. When factories and workshops can produce spare or replacement parts on demand, they can run more efficiently, with a smaller carbon footprint and less waste. For example, some of our customers operate on a “take one, make one” policy, where small numbers of spare or replacement parts are digitally stored and can be quickly 3D printed to ensure that day-to-day operations continue without disruption.